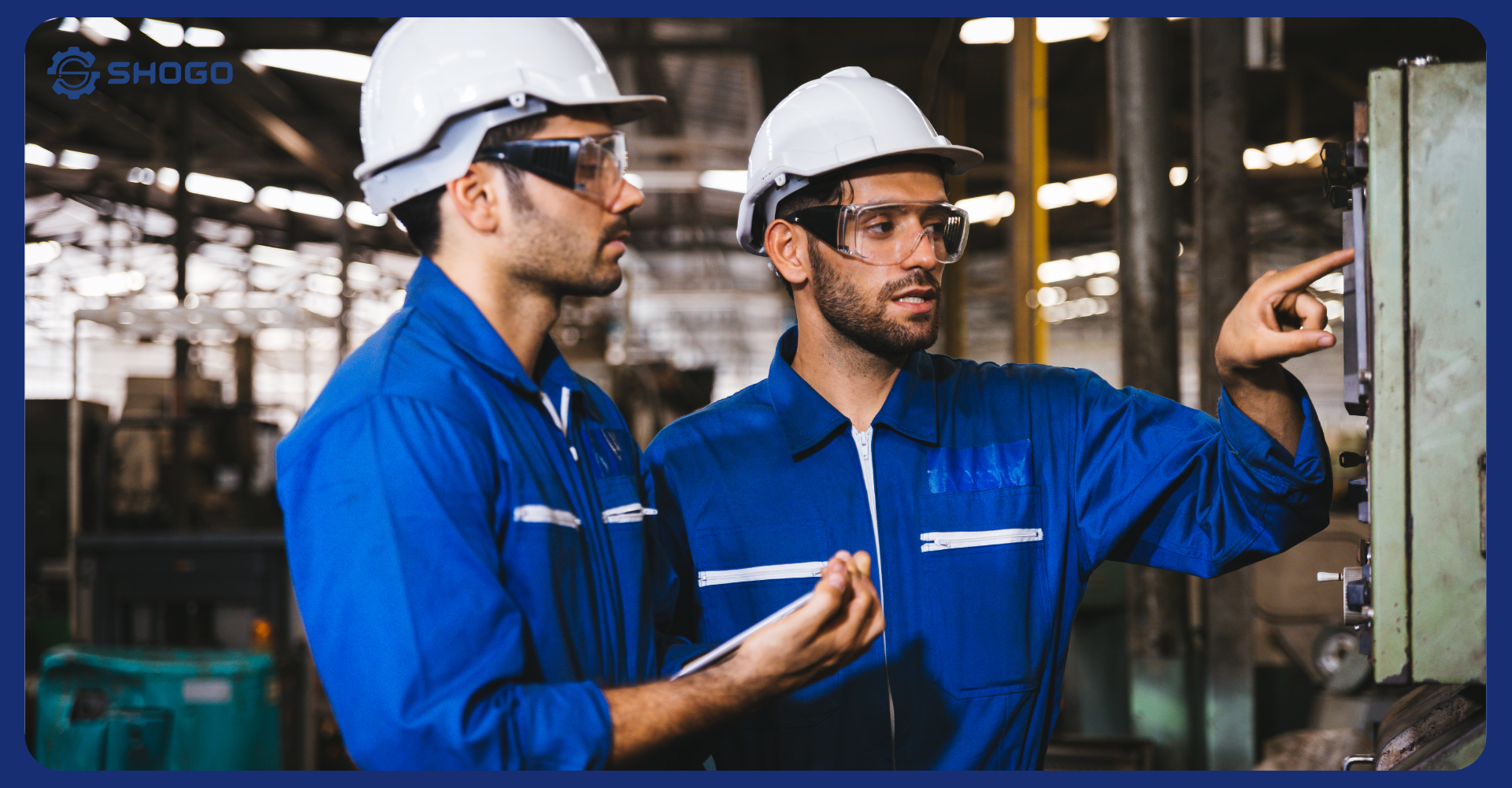
1. Introduction
Busbars play a crucial role in electrical systems, facilitating the transmission of electrical energy from the source to various consuming devices. Operating in a high-voltage environment, busbars are susceptible to various damages that can impact the system’s safety and operational efficiency. Therefore, regular busbar maintenance and repair are essential to ensure optimal performance and longevity. This comprehensive guide will provide you with effective busbar maintenance and repair methods to enhance safety, improve efficiency, and extend the lifespan of your electrical system.
2. Significance of Busbar Maintenance and Repair
Regular busbar maintenance and repair offer a multitude of practical benefits, including:
- Ensuring Operational Safety: Busbars operate at high voltages. Periodic maintenance and repair help detect and promptly address potential hazards such as cracks, rust, loose connections, and more, preventing the risk of electrical fires, explosions, and ensuring the safety of personnel and equipment.
- Enhancing Operational Efficiency: Maintenance and repair procedures eliminate dirt, rust, and other contaminants, enhancing the busbar’s conductivity, reducing energy losses, and optimizing the overall efficiency of the electrical system.
- Extending Busbar and System Lifespan: Regular maintenance and repair enable early detection of aging and deterioration, allowing for timely corrective actions that extend the busbar’s and system’s lifespan, minimizing replacement costs.
3. Busbar Maintenance and Repair Schedule
The frequency of busbar maintenance and repair depends on various factors, including the operating environment, system load, and manufacturer recommendations. However, a general schedule is typically recommended as follows:
- Daily Inspection: Visually inspect the busbars for any abnormalities such as cracks, rust, deformation, or discoloration.
- Periodic Inspection:
- Monthly: Clean the busbars, check connections, and tighten bolts and screws.
- Quarterly: Measure insulation resistance and inspect busbar temperature using thermal imaging cameras.
- Annually: Conduct a comprehensive busbar inspection, including mechanical, electrical, and insulation checks.
- Unscheduled Inspection: Perform immediate inspection following any incidents or upon detecting unusual signs.
4. Effective Busbar Maintenance and Repair Methods
Here’s a detailed breakdown of effective busbar maintenance and repair procedures:
4.1. Busbar Cleaning
- Removing Dust and Cobwebs: Utilize a vacuum cleaner or soft cloth to carefully remove accumulated dust and cobwebs from the busbar surfaces.
- Cleaning the Busbars: Employ a diluted cleaning solution specifically recommended by the manufacturer to clean the busbars. Avoid using flammable solvents or harsh acidic or alkaline cleaners that could damage the insulating coating.
- Drying the Busbars: After cleaning, use a clean cloth to thoroughly dry the busbars and allow them to air dry completely.
4.2. Connection Inspection
- Checking Bolts and Screws: Inspect bolts and screws for any signs of looseness or rust. Use appropriate wrenches to tighten them if necessary.
- Contact Point Inspection: Ensure that contact points between busbars and other equipment are clean and secure. Apply specialized lubricating grease to contact points if required.
4.3. Insulation Resistance Measurement
- Using an Insulation Resistance Tester: Employ a dedicated insulation resistance tester to measure the insulation resistance between the busbar and the enclosure, as well as between individual busbar conductors.
- Comparing Measured Values to Permissible Limits: The measured insulation resistance values must meet or exceed the permissible limits specified by the manufacturer. If the measured values fall below the permissible limits, further investigation is necessary.
4.4. Temperature Inspection
- Utilizing Thermal Imaging Cameras: Employ thermal imaging cameras to measure the busbar temperature during operation.
- Comparing Measured Temperatures to Permissible Limits: The measured busbar temperatures must not exceed the permissible limits set by the manufacturer. If excessive temperatures are detected, identify and address the underlying causes.
4.5. Mechanical Inspection
- Checking for Deformation: Inspect the busbars for any signs of warping or bending.
- Checking for Cracks: Carefully examine the busbar surfaces for cracks or fractures.
- Checking for Vibration and Noise: During busbar operation, check for excessive vibration or unusual noises.
4.6. Electrical Inspection
- Voltage Inspection: Utilize a voltmeter to measure the voltage across the busbars.
- Current Inspection: Employ an ammeter to measure the current flowing through the busbars.
- Voltage Drop Inspection: Check for voltage drops across connections.
4.7. Documentation
- Recording Inspection and Repair Results: Thoroughly document the outcomes of busbar inspections and repairs in a dedicated logbook or data sheet.
- Maintaining Maintenance and Repair Records: Preserve maintenance and repair records for future reference, enabling the monitoring of busbar condition and the planning of subsequent maintenance and repair activities.
5. Essential Safety Precautions for Busbar Maintenance and Repair
- Occupational Safety: Prior to commencing any busbar maintenance or repair activities, ensure you possess adequate knowledge, skills, and appropriate personal protective equipment (PPE).
- Adherence to Procedures: Strictly follow the busbar maintenance and repair procedures recommended by the manufacturer or as mandated by governing regulations.
- Utilization of Proper Tools: Employ specialized tools designed specifically for busbar maintenance and repair tasks.
- Post-Maintenance Cleaning: Upon completion of maintenance or repair work, thoroughly clean the work area and neatly organize all tools and equipment.
6. Benefits of Regular Busbar Maintenance and Repair
Regular busbar maintenance and repair offer a multitude of tangible benefits, including:
- Enhanced System Safety: Minimize the risk of electrical fires and explosions, ensuring the safety of personnel and equipment.
- Improved System Efficiency: Enhance the busbar’s conductivity, reduce energy losses, and optimize the overall efficiency of the electrical system.
- Extended Busbar and System Lifespan: Promptly detect and address signs of wear and tear or aging, extending the lifespan of the busbar and the electrical system, minimizing replacement costs.
- Cost Savings: Prevent the occurrence of severe damage that could lead to costly repairs or replacements.
7. Conclusion
Regular busbar maintenance and repair are crucial for ensuring the safe operation, efficient performance, and extended lifespan of your electrical system. By adhering to proper procedures and employing effective maintenance and repair methods, you can minimize costs and safeguard the integrity of your electrical system.
Why choose SHOGO Viet Nam?
1. Quality Commitment: SHOGO Viet Nam.,JSC is the No. 1 Busbar and Cable manufacturer in Viet Nam for the new energy industry. We are committed to providing our customers with products of the highest quality standards. All raw materials are inspected for quality before production, and 100% of products are thoroughly inspected before delivery. SHOGO Viet Nam holds prestigious certificates: IATF16949-2016, ISO 9001-2015, ISO 14001-2015, ISO/IEC 17025-2017,…
2. Competitive Pricing: With a team of experienced engineers who have participated in many electric vehicle production projects, SHOGO Viet Nam can provide product consulting to help customers optimize production costs and improve product quality. With a geographical location that is convenient for trading, along with modern machinery and technology, SHOGO Viet Nam can provide products at the most competitive prices on the market.
3. Dedicated Service: With a team of experienced employees, large production capacity and reasonable supply, SHOGO Viet Nam always ensures on-time delivery for customers. Support customers in all projects, quickly handle arising problems.
You can refer to some of our Busbar products on the page “PRODUCTS“.
To receive FREE CONSULTATION on our products, Busbar design and manufacturing services, please CONTACT
Email: info@shogovn.com / info@shogobusbar.com
Whatsapp / Wechat / Zalo : +84 989538022/ +84 393929885