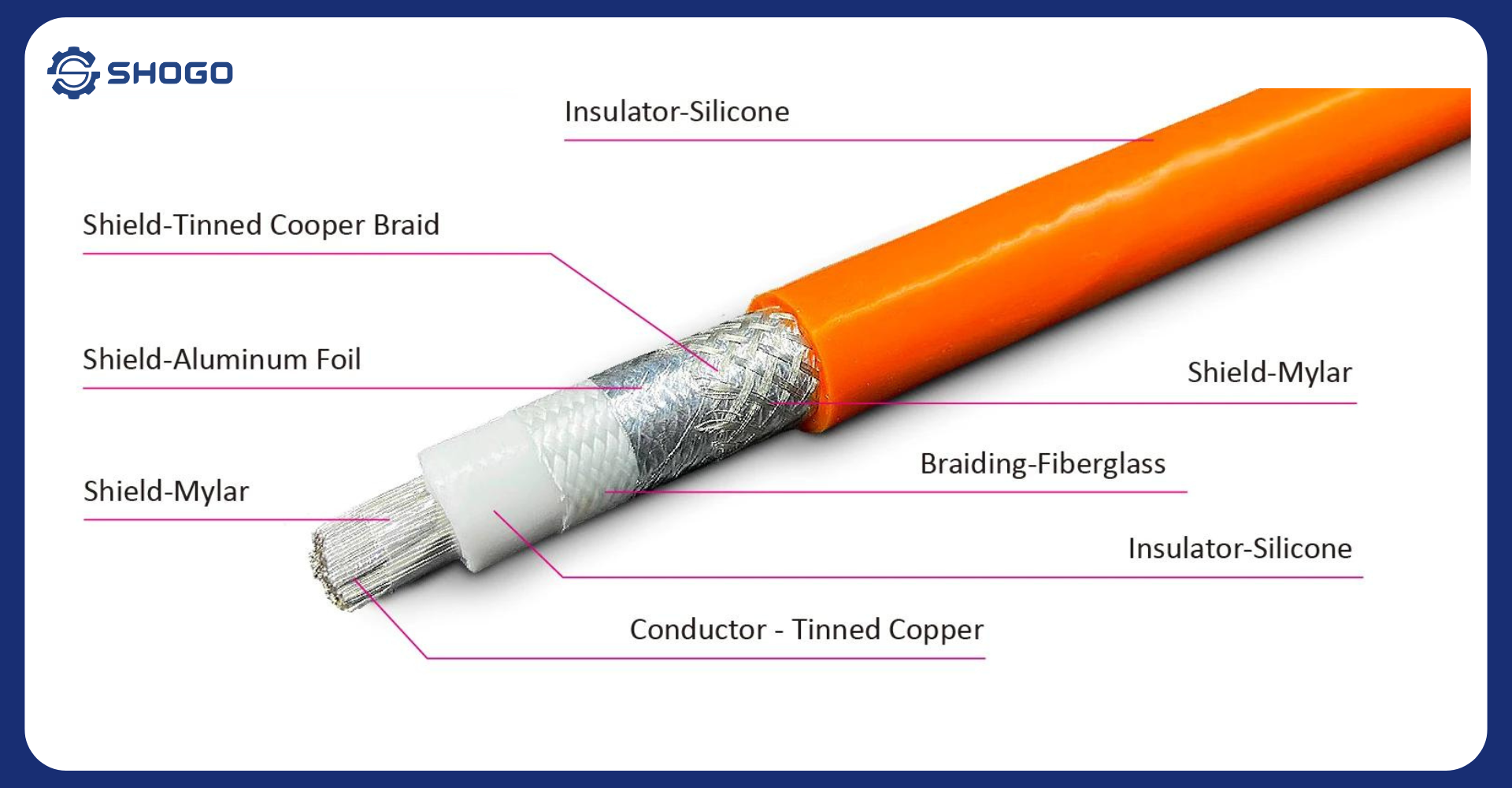
4. Protective Layer of High Voltage Cable Connections
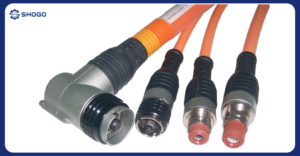
The connection between a High Voltage (HV) cable and its termination is a potential weak point in an electrical system. Therefore, ensuring a protective layer at these connections is crucial to preventing failures, ensuring operator safety, and maintaining system stability.
Role of the Protective Layer:
- Preventing electrical discharge: The protective layer prevents discharge between phases, between the cable core and sheath, or between contacting metal parts.
- Moisture resistance: Protects the connection from humid environments, preventing the formation of leakage currents.
- Corrosion resistance: Prevents corrosive agents from the external environment from affecting the metal components of the connection.
- Resistance to mechanical impacts: Protects the connection from external mechanical impacts such as collisions and vibrations.
- Insulation: Ensures good insulation between parts with different voltages in the connection.
Common Protective Materials:
- Rubber compounds: Have good elasticity, can withstand high temperatures, are moisture-resistant, and oil-resistant.
- Epoxy: High mechanical strength, good heat resistance, and good chemical resistance.
- Silicone: Withstands high temperatures, has good chemical stability, and high resistance to aging.
- Tape: Used to fix the protective layers, forming a sealed membrane.
Protective Layer Application Methods:
- Casting method: Pouring the protective compound into a prepared mold and then curing it.
- Wrapping method: Wrapping the connection surface with layers of tape or fabric impregnated with a protective compound.
- Spraying method: Spraying the protective compound onto the connection surface using a specialized spray gun.
Requirements for the Protective Layer:
- High mechanical strength: Withstands mechanical impacts during transportation, installation, and operation.
- Good elasticity: Can expand and contract to adapt to the thermal expansion of materials.
- Good heat resistance: Withstands high temperatures during operation.
- Good electrical insulation: Ensures complete insulation between parts with different voltages.
- Resistance to moisture and corrosion: Protects the connection from environmental effects.
The protective layer of a high-voltage cable connection plays a crucial role in ensuring the stability and safety of the electrical system. Selecting the appropriate materials, application methods, and quality inspection of the protective layer is essential to ensure the service life and operating efficiency of the connection.
5. Electromagnetic Shielding in High-Voltage Connectors
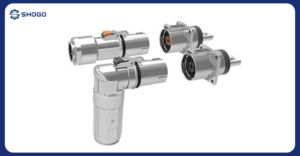
Electromagnetic shielding is an indispensable component in High Voltage (HV) connectors. It acts as a protective barrier, preventing external electromagnetic interference from penetrating the connector and affecting the operation of electronic components. Simultaneously, the shield prevents electromagnetic interference generated from within the connector from spreading to the surrounding environment, causing interference with other devices.
Why is electromagnetic shielding important?
- Preventing external interference: In automotive environments, electronic devices operate at high density, creating numerous sources of electromagnetic interference. Shielding minimizes the impact of this interference, ensuring the stable operation of electronic systems such as ABS, ESP, infotainment systems, etc.
- Improving reliability: By reducing interference, shielding enhances the reliability of HV connectors, minimizing malfunctions and increasing the lifespan of the device.
- Ensuring stable power transmission: Especially in electric vehicle applications, shielding plays a crucial role in ensuring stable power transmission between the vehicle and the charging station, preventing interruptions or disconnections.
- Meeting stringent standards: The automotive industry sets high standards for the reliability and safety of products. Electromagnetic shielding is a critical factor in helping products meet these standards.
Factors affecting the effectiveness of electromagnetic shielding
- Materials: Materials commonly used for shielding include metals (copper, aluminum), alloys, or conductive composites. Each material has different advantages and limitations in terms of shielding effectiveness, durability, cost, etc.
- Structure: The structure of the shield includes its shape, size, thickness, and method of connection to other parts of the connector. A rational shield structure will help optimize interference shielding effectiveness.
- Contact size and shape: The size and shape of the contacts affect the conductivity and electric field distribution within the connector, thereby affecting the effectiveness of the shield.
- Enclosure: The connector’s enclosure also plays a crucial role in protecting the shield and internal components from environmental impacts.
The automotive industry has stringent requirements for electromagnetic shielding, such as heat resistance and durability.
- shape of the electromagnetic shield
- types of materials used for shielding purposes
- size, thickness, shape, and structure of contacts and enclosures
All these factors determine the level of electromagnetic interference they can block and affect their shielding effectiveness. They must be considered during the design and manufacturing process when creating an effective shielding design that meets industry standards.
Electromagnetic shielding is a critical technology that plays an indispensable role in ensuring the stable and reliable operation of high-voltage connectors, especially in the automotive industry. With the continuous development of electronic technology, the demand for effective interference shielding solutions is increasing. Research and development of new types of shields with higher performance and lower costs will be a promising direction in the future.
6. Conclusion
Designing a High Voltage cable shielding system for electric vehicles is a process that requires a harmonious combination of technical and safety factors. Selecting suitable materials, designing an optimal structure, and applying new technologies will help ensure the safety and high performance of electric vehicles.